Re: Fostek's R&D department
Few bits and pieces guys, but nothing major. Technically it could go down on it's wheels now, but I still haven't got any wheels. It's more or less ready to go away for wiring loom now; just 1 or 2 odds and sods to sort out (like wheel speed sensors, for instance - haven't even looked at these yet and they'll need to be in place as they're an integral part of the car's electrickery)
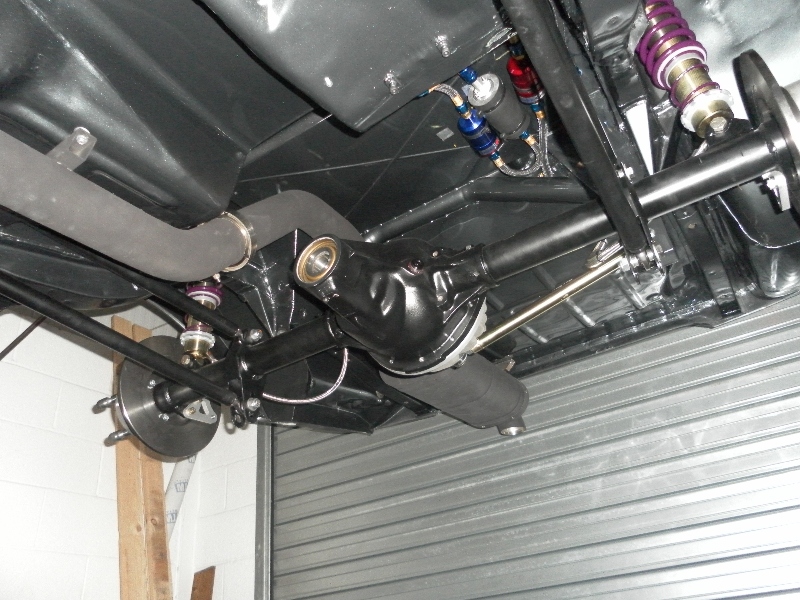
Biggest step forward was the rear dampers showing up; this meant we could lift the axle (this is a dummy/test axle) into place, along with some hubs and things so we can put wheels on. I ordered the dampers with some extra long hoses so the reservoirs could be mounted in the boot. This meant taking a holesaw to the boot floor; not my favourite job! Great solution though. The rest of the exhaust system is on, fitted a treat. Notice the tail pipe pointing at the ground in an attempt to "help" get the car through noise test!
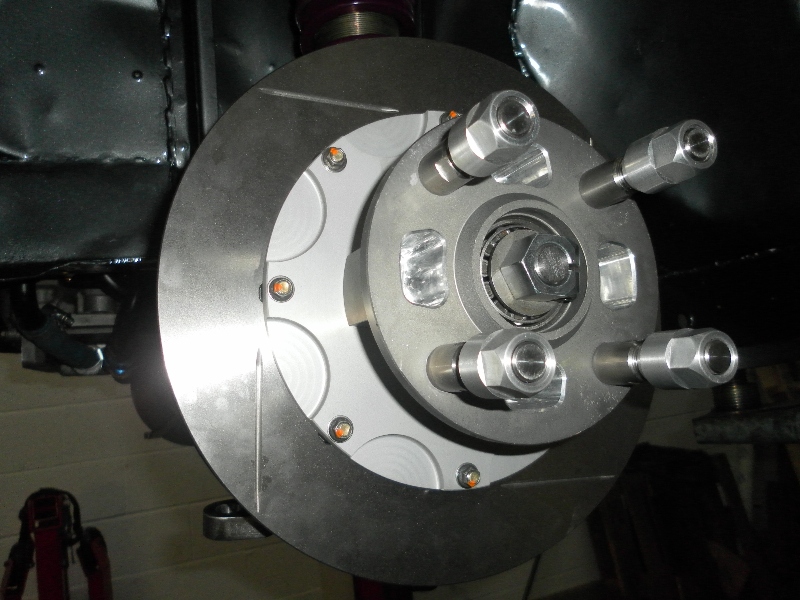
The front end is now together enough to get wheels on... Uprights, steering arms, hubs, bells, discs etc. Still waiting for caliper brackets, they will probably have to go on after the car's wired now. Not a problem, it doesn't need working brakes for wiring.
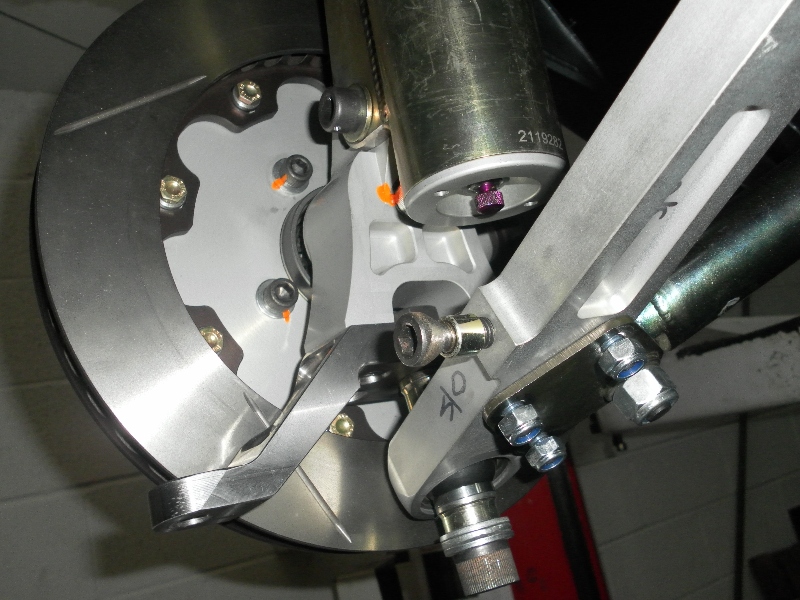
Axle @ full droop.
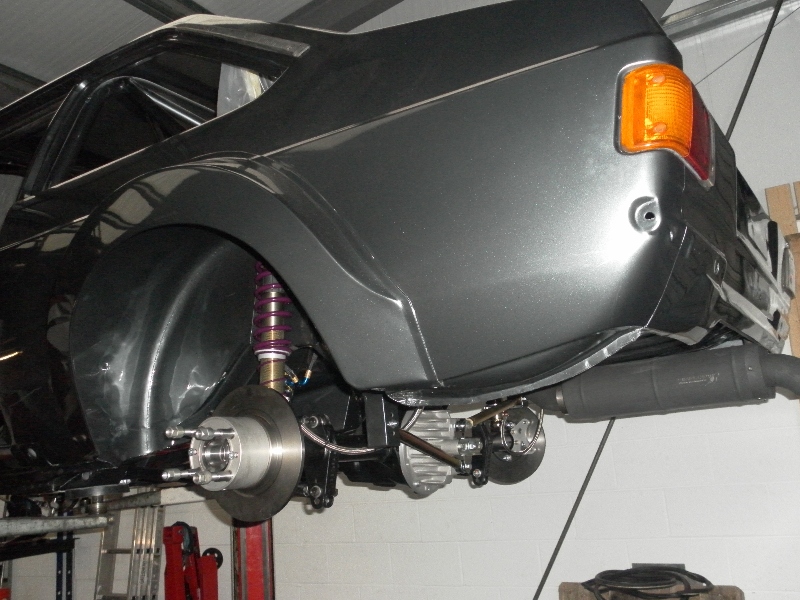
This is the compressor that supplies compressed air for the gearshift system. There's 2 systems built into the car; the first system (for long rallies, or should I say rallies with long sections between service) uses this compressor to fill an accumulator with compressed air, at a fairly low pressure. Compressor runs off the 12v car electrics = no limit to number of gearshifts. However, for short "sprint" type events (on a lot of rallies these days, you'll be doing 10 miles between services max) then we can ditch the compressor and charge the receiver to 300bar, along with an extra regulator to drop the 300bar to a workable pressure. This is the norm on sprint/hillclimb cars, but my theory is a single venue rally is no different to a series of sprints linked together. We can charge the bottle (or swap it for a fully charged bottle) in service.
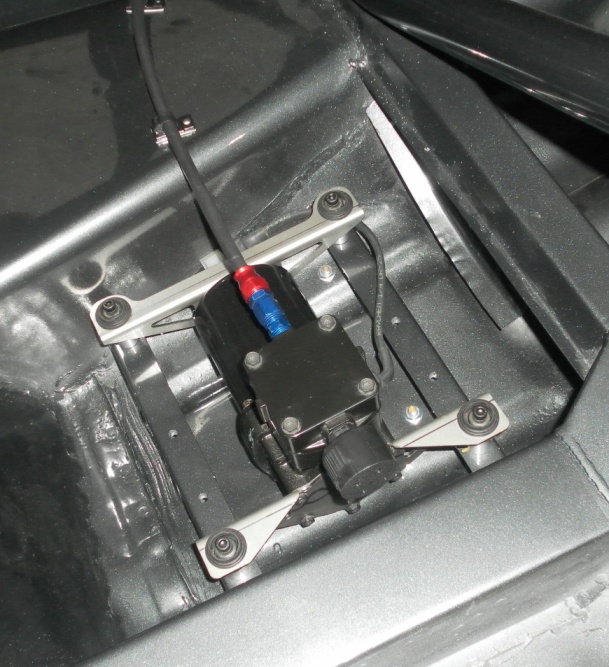
This bizarre looking manifold houses the various in/outlets from the air tank. There's 5 different threads in the manifold, and they're all different! Took some working out.
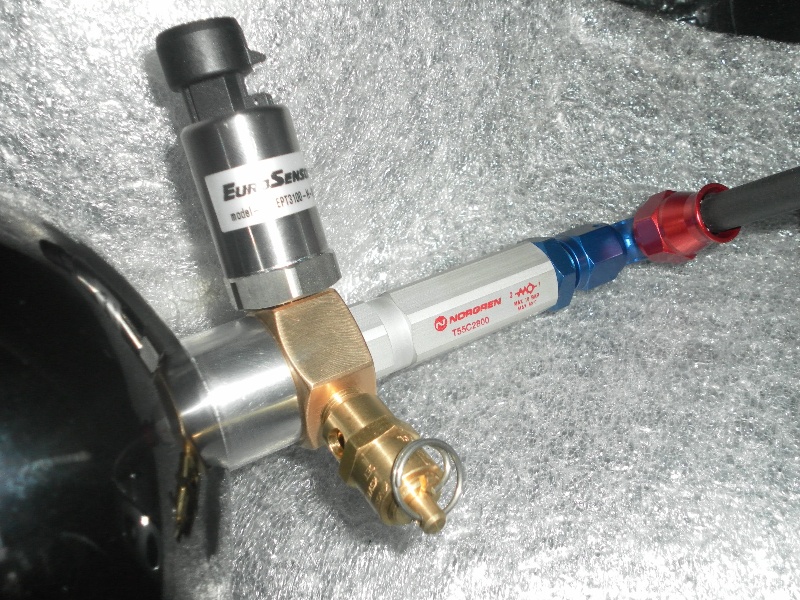
I nearly forgot a catch tank for the engine bay. Fairly standard-issue alloy tank, although I wanted to use these push-fit fittings for the breather pipe.
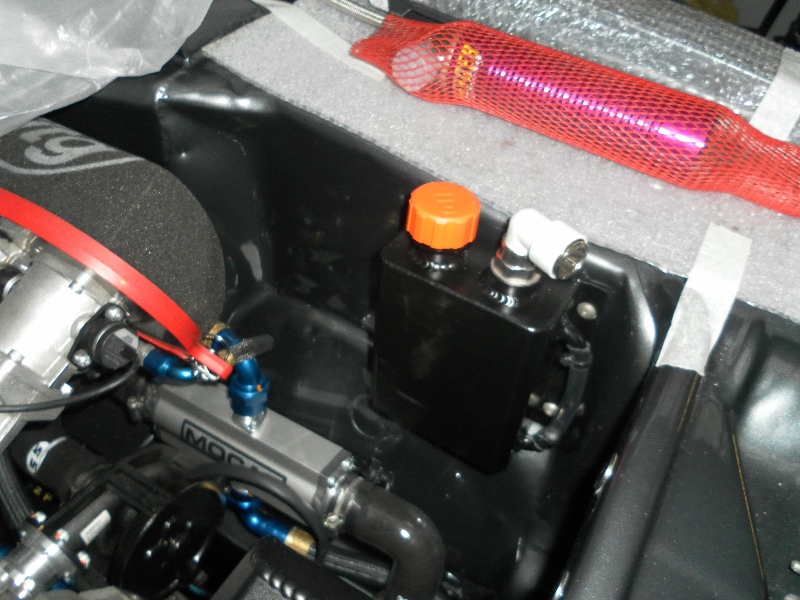
And this is why: the breather comes out the centre of the oil tank filler cap. To unscrew the cap would mean disconnecting the hose (or engineering a swivel of some sort) whereby these push-in fittings are "swivel elbows" anyway - you can unscrew the cap and the fitting stays still. Cool or what?
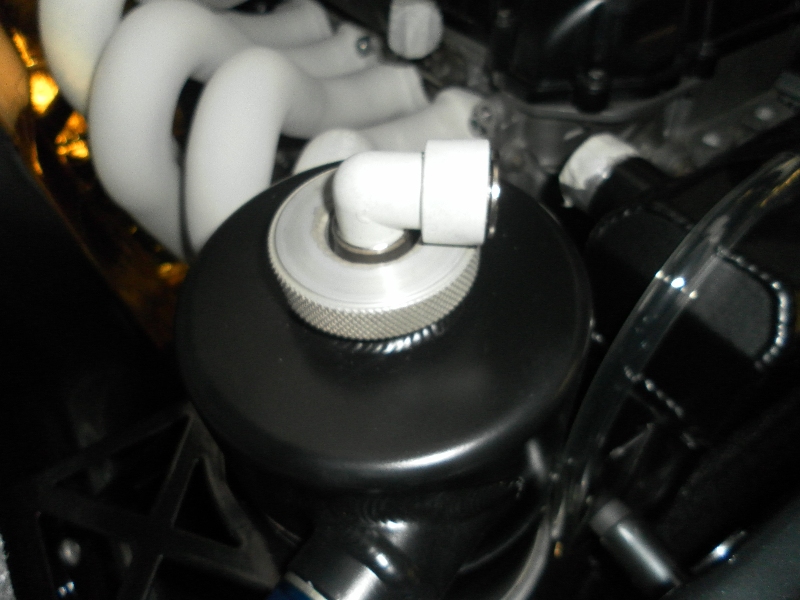
That's it for today. Next update should see the car on the deck!
Few bits and pieces guys, but nothing major. Technically it could go down on it's wheels now, but I still haven't got any wheels. It's more or less ready to go away for wiring loom now; just 1 or 2 odds and sods to sort out (like wheel speed sensors, for instance - haven't even looked at these yet and they'll need to be in place as they're an integral part of the car's electrickery)
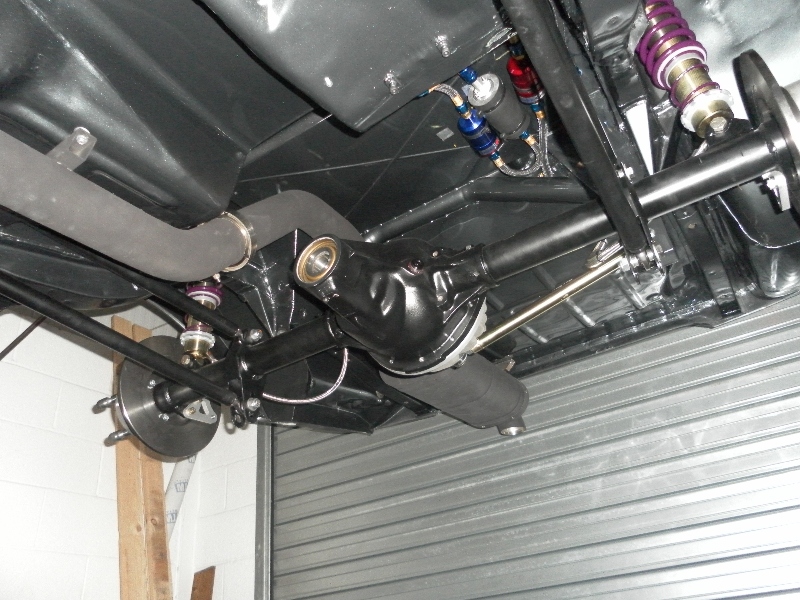
Biggest step forward was the rear dampers showing up; this meant we could lift the axle (this is a dummy/test axle) into place, along with some hubs and things so we can put wheels on. I ordered the dampers with some extra long hoses so the reservoirs could be mounted in the boot. This meant taking a holesaw to the boot floor; not my favourite job! Great solution though. The rest of the exhaust system is on, fitted a treat. Notice the tail pipe pointing at the ground in an attempt to "help" get the car through noise test!
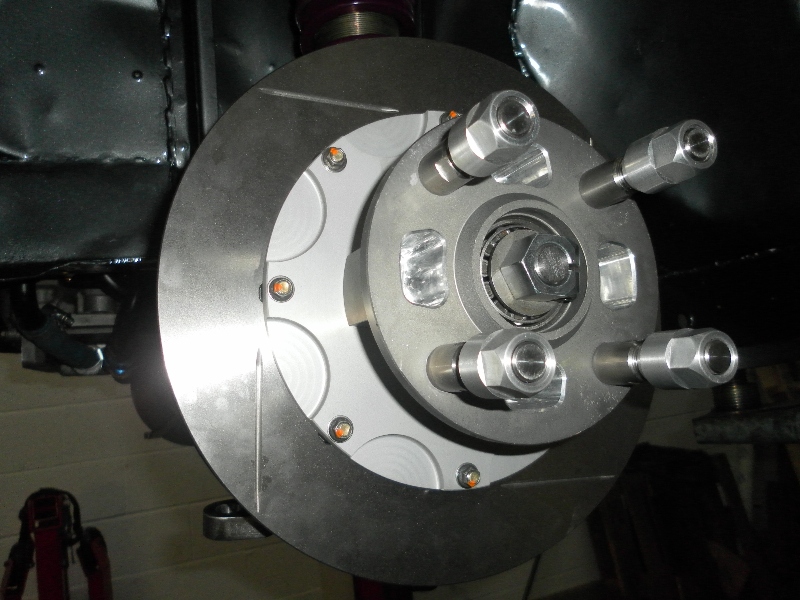
The front end is now together enough to get wheels on... Uprights, steering arms, hubs, bells, discs etc. Still waiting for caliper brackets, they will probably have to go on after the car's wired now. Not a problem, it doesn't need working brakes for wiring.
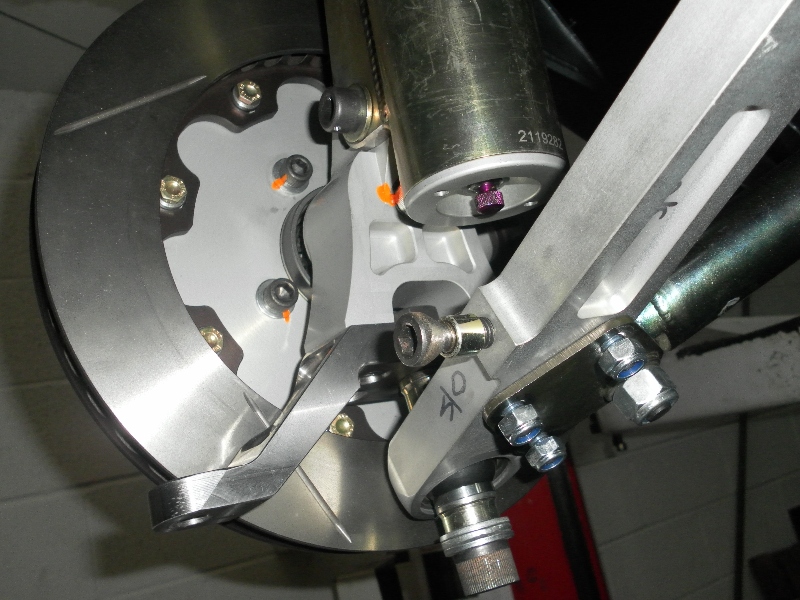
Axle @ full droop.
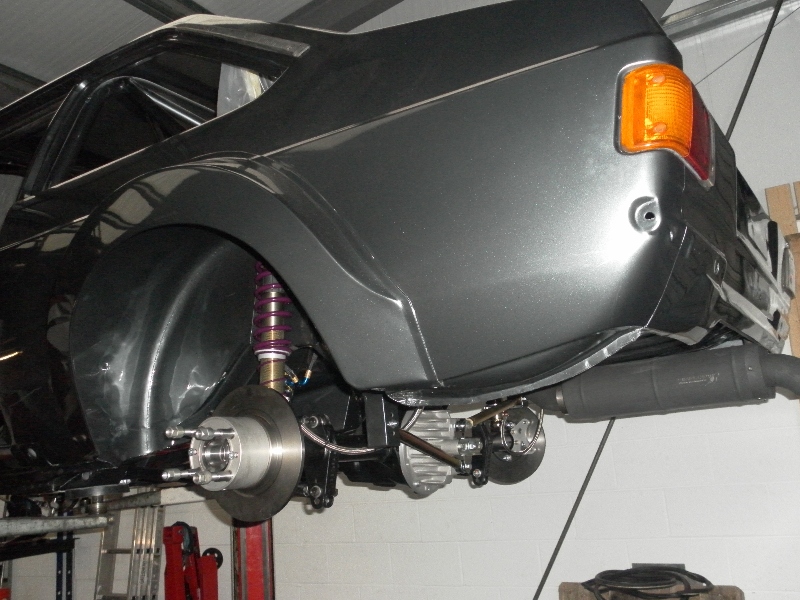
This is the compressor that supplies compressed air for the gearshift system. There's 2 systems built into the car; the first system (for long rallies, or should I say rallies with long sections between service) uses this compressor to fill an accumulator with compressed air, at a fairly low pressure. Compressor runs off the 12v car electrics = no limit to number of gearshifts. However, for short "sprint" type events (on a lot of rallies these days, you'll be doing 10 miles between services max) then we can ditch the compressor and charge the receiver to 300bar, along with an extra regulator to drop the 300bar to a workable pressure. This is the norm on sprint/hillclimb cars, but my theory is a single venue rally is no different to a series of sprints linked together. We can charge the bottle (or swap it for a fully charged bottle) in service.
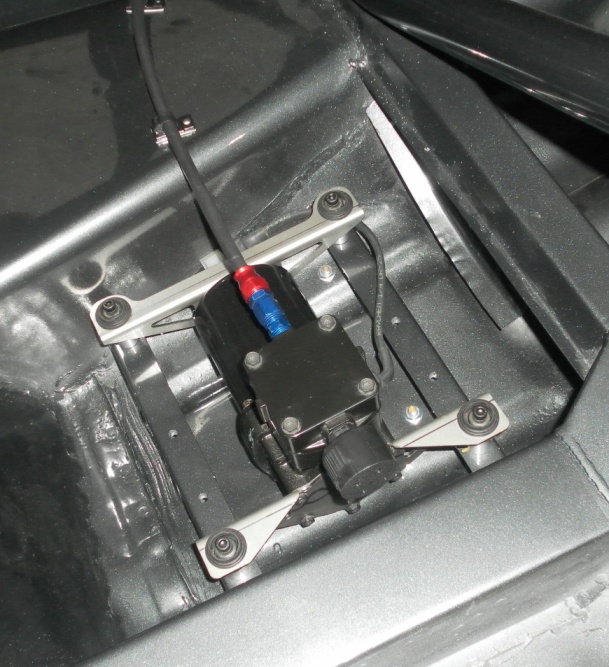
This bizarre looking manifold houses the various in/outlets from the air tank. There's 5 different threads in the manifold, and they're all different! Took some working out.
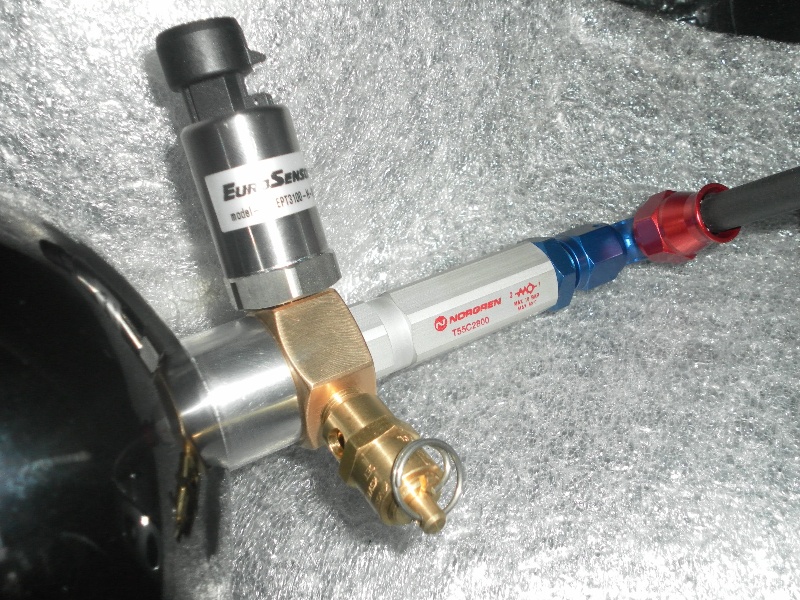
I nearly forgot a catch tank for the engine bay. Fairly standard-issue alloy tank, although I wanted to use these push-fit fittings for the breather pipe.
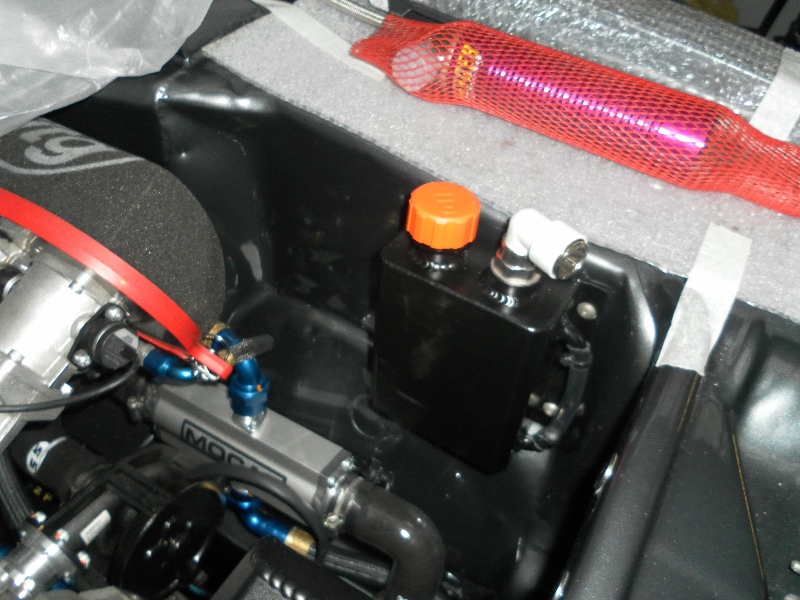
And this is why: the breather comes out the centre of the oil tank filler cap. To unscrew the cap would mean disconnecting the hose (or engineering a swivel of some sort) whereby these push-in fittings are "swivel elbows" anyway - you can unscrew the cap and the fitting stays still. Cool or what?
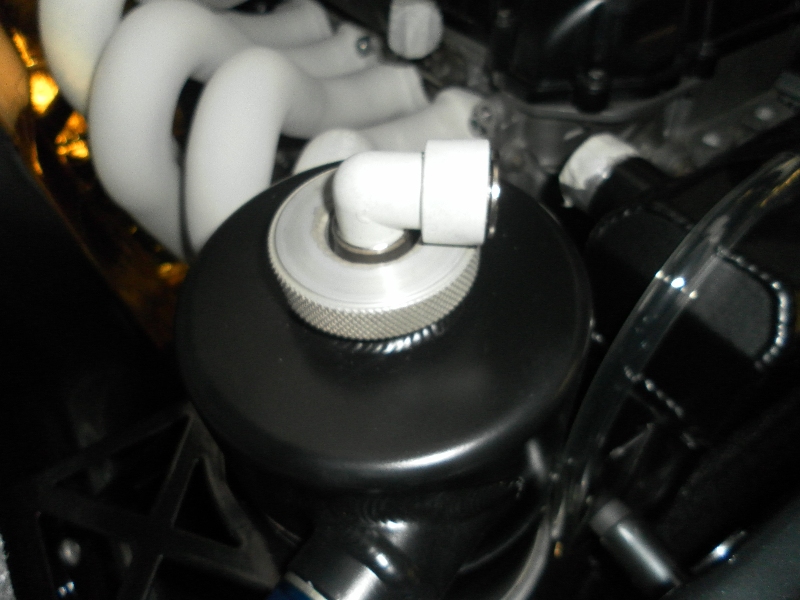
That's it for today. Next update should see the car on the deck!
Comment